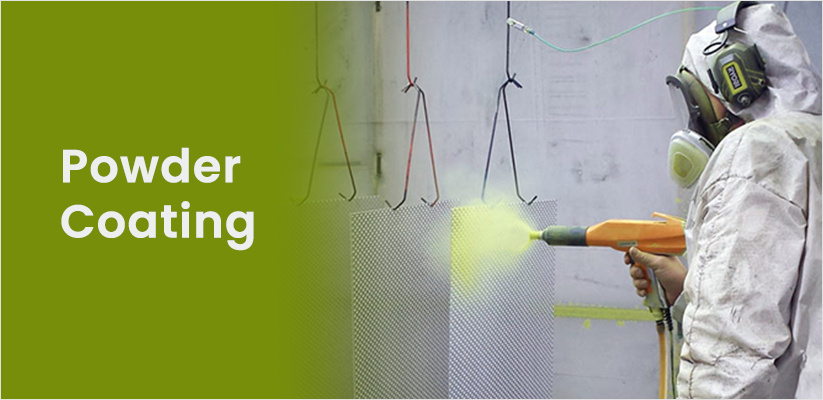
Why Pre-Cure Cooling in Powder Coating Ovens Is Essential for Certain Substrates
Powder coating might seem straightforward—heat the substrate, cure the coating, and voilà! A perfect finish. But behind the scenes, achieving that flawless and durable result often involves a lesser-known but critical step: pre-cure cooling. This phase can make all the difference, especially when dealing with specific substrates. If you’ve ever wondered why some powder coating processes take extra care with cooling before curing, here’s the inside scoop.
Preventing Warping in Heat-sensitive Substrates with Gradual Temperature Adjustments
Heat-sensitive materials like plastics or thin metals can be tricky to coat because they don’t handle sudden temperature changes well. Jumping straight into high temperatures in a powder coating oven can cause these materials to warp, sag, or even crack. That’s where pre-cure cooling steps in to save the day.
By gradually adjusting the temperature, reliable powder coating ovens allow these substrates to acclimate without being overwhelmed. This careful process ensures the material retains its shape and integrity while preparing it for the final cure. Whether you’re working with compact powder coating ovens or larger industrial models, pre-cure cooling is a crucial step for any project involving delicate or heat-sensitive materials.
Maintaining Adhesion Integrity by Stabilizing the Coating Before Full Cure
When powder coating is applied, the particles begin to adhere to the substrate at lower temperatures before fully bonding during curing. Rushing this process by skipping pre-cure cooling can jeopardize that crucial initial adhesion phase.
Quality powder coating ovens with pre-cooling features allow the coating to stabilize, ensuring it grips the surface properly. Without this step, the bond between the coating and the substrate can weaken, leading to issues like peeling, flaking, or uneven finishes later. A controlled pre-cure environment not only enhances adhesion but also guarantees that the final result stands the test of time.
Reducing Thermal Stress in Multi-layered or Composite Materials
Composite materials or those with multiple layers often behave unpredictably under intense heat. Each layer can expand or contract at different rates, creating internal stresses that might result in cracking, delamination, or other structural issues. Pre-cure cooling provides a buffer that helps minimize these risks.
Reliable powder coating ovens with precise temperature controls play a pivotal role in managing thermal stress. They allow the entire material to adjust gradually, ensuring all layers remain intact and cohesive. This step is especially critical for industries where composite materials are the norm, as it directly impacts both durability and aesthetics.
Enhancing Coating Uniformity by Minimizing Pre-cure Surface Fluctuations
Achieving a smooth, even coating requires more than just a skilled application. The substrate itself must remain stable throughout the process, and pre-cure cooling is key to making that happen. Without it, rapid temperature changes can cause surface irregularities like bubbling, rippling, or uneven texture.
By introducing a controlled cooling interval, powder coating ovens help maintain a steady substrate surface before the full curing phase begins. This not only ensures uniformity in the coating but also reduces the likelihood of defects that could compromise the final product’s appearance or performance. It’s a simple step that elevates the entire powder coating process.
Protecting Delicate Substrate Finishes from Premature Curing Effects
Certain substrates come with pre-existing finishes or coatings that are vulnerable to heat. Premature curing can cause discoloration, melting, or even complete destruction of these delicate finishes. Pre-cure cooling serves as a protective measure, ensuring the integrity of the substrate while allowing the powder coating to set gradually.
Compact powder coating ovens equipped with pre-cooling capabilities are especially useful for smaller, intricate projects where precision is paramount. This process ensures that both the substrate and the new coating come out looking flawless, with no unexpected surprises due to premature exposure to high temperatures.
Optimizing Overall Process Efficiency with Controlled Cooling Intervals
Efficiency is everything in the powder coating world. Skipping pre-cure cooling might seem like a time-saver, but it often results in defects or rework that can slow down production and inflate costs. Incorporating controlled cooling intervals into the process ensures a smoother workflow and fewer mistakes.
Modern, quality powder coating ovens are designed to balance precision with efficiency. By integrating pre-cooling steps, they create an optimized system where substrates are prepared properly, coatings adhere better, and the need for touch-ups is dramatically reduced. In the end, this saves both time and resources, making the entire process more cost-effective and reliable.